Main OPAMPs (IC1 and IC2) might be damaged if the output voltage of IC1 or IC2 differs from a typical value in the manual. Furthermore, you can observe signals around OPAMPs.
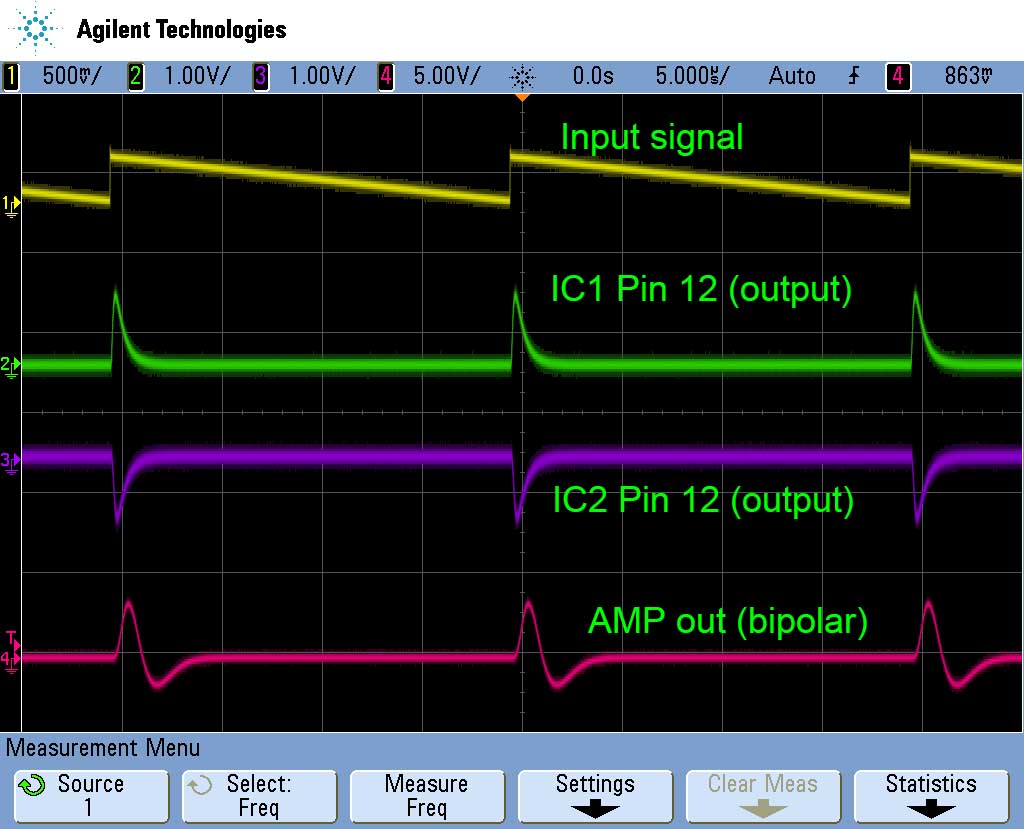
CA3030A has been discontinued, and it is not easy to obtain it. CA3030A can be electronically replaced with a modern OPAMP, keeping compensation pins unconnected. However, its pin configuration differs from that of a modern single OPAMP. A TO-99 metal might be usable for replacement, but a TO-99 package is also uncommon now. Therefore, I made the conversion PCB to use the standard 8-lead SOIC package OPAMP.
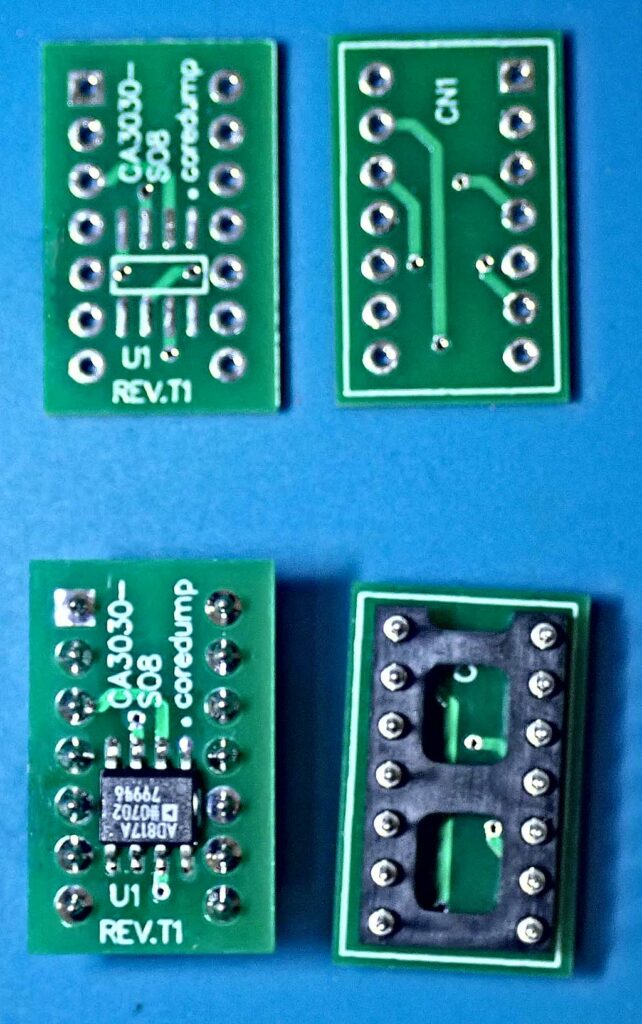
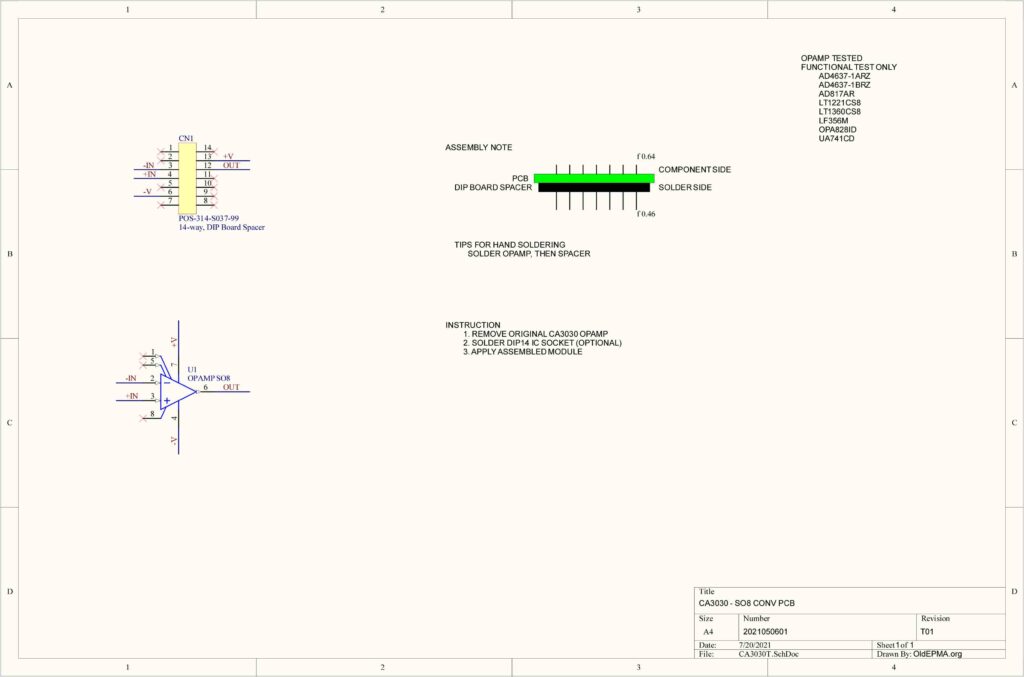
I soldered IC sockets. Therefore, the conversion module is replaceable.